– Dewatering
– Swabbing
– Dry air or nitrogen
– Vacuümdrying
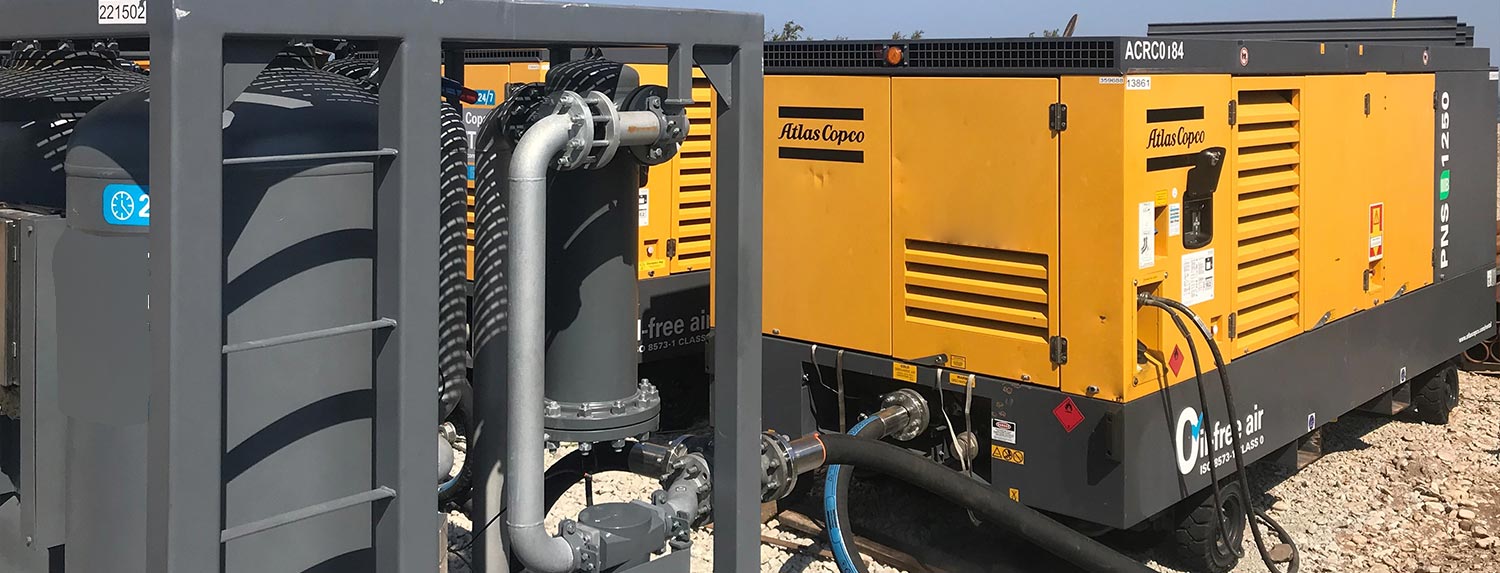
Because water does not pose a direct threat to humans and animals and is easy to obtain, many pipeline activities use this liquid for testing and pigging. Although water may seem harmless, it can still have adverse consequences.
- Hydrate formation;
- Increase corrosion;
- Product contamination;
- Water hammer.
Water residue in a gas pipe can form methane hydrates. This is a solid substance that can eventually block your gas transport. In addition, water in uncoated steel pipelines and in combination with sufficient oxygen can cause corrosion. Water can:
- form corrosion:
- reduce the wall thickness and harm the integrity of the pipeline;
- free flowing (rust) particles can damage e.g. turbines and instrumentation;
- pollute or change the specification of your product;
- cause a hydraulic shock (water hammer) that can damage your equipment.
Enough reasons to make sure that your pipeline will be free of water. Depending on the requirements and your wishes, TECCURO has various options to support you in this.
Draining
TECCURO has various options for dewatering pipelines. The first and most important step is to properly drain your pipeline or pipe system. Pipes on a process plant often have fixed vent and drain points that can be used for this purpose. Transport pipelines often do not have these drain points, but can often be pigged.
Swabbing
Bi-directional (BiDi) pigs can be used for displacing the water. These pigs are usually pushed with compressed air or nitrogen. The water, accumulated in front of the pig, will be pushed to the outlet of the pipeline. In some cases or in combination with BiDi pigs, TECCURO suggest the use of foam pigs. These pigs act like a sponge and can easily absorb the free water. This process is also referred to as swabbing a pipeline.
Drying
If the pipeline has being swabbed, most of the free water has been removed. This does not mean that the pipe (system) is dry. Depending on the wishes you have as a customer, TECCURO can advise which drying method is the most effective and efficient. Pipelines that transport cryogenic products, in contrast to oil pipes, often have to be dried to a very low dew point. TECCURO has three different drying options for lowering the dew point in your pipeline:
- dry (hot) air;
- dry (hot) nitrogen;
- Vacuum drying.
“The dew point is the temperature in which water vapor starts to condense by cooling the air, and without moisture being added or removed. As soon as the air reaches the dew point temperature, the air will be saturated with water vapor. The relative humidity is then 100 percent.” (Source: Royal Netherlands Meteorological Institute)
Dry air
The “wet” outside air is dried via a drying system (pressure swing absorber) and blown through the pipeline via a temporary pipeline system. The dry air ensures that the water in the pipeline can evaporate and is transported to the exit. This process will last until the moisture content in the pipeline is as desired. A saturation period will be used to ensure that the system is dry (the desired dew point has been reached). In this case the system will be closed for a certain period of time. If there is still (too) much moisture in the system, this moisture will evaporate and causes the dew point to rise. After this, it is necessary to resume drying until the dew point, after the saturation period, remains sufficiently stable. The dry air can easily be heated to speed up the drying process. The warm dry air not only contains more absorption capacity, but also accelerates the evaporation process, which will shorten the drying time.
Nitrogen drying
As with dry air, the drier gaseous nitrogen is also blown through the pipeline to evaporate the remaining water. In addition to a lower dew point, Nitrogen (inert) also has the property of reducing the oxygen level and thus preserving the pipeline.
Vacuum drying
In contrast to drying with air and nitrogen, vacuum drying is based on a different drying technique. TECCURO has a lot of knowledge about this method, in which the boiling point is lowered until the water in the pipeline starts to boil at the prevailing ambient temperature. The advantages of vacuum drying are:
- Suitable for complex systems (which are difficult to dry with air or nitrogen);
- Deep dew points down to about -80 °C are possible;
- Relatively simple equipment with low fuel consumption.
The limitations of vacuum drying are that the drying process depends on the ambient temperature and therefore the drying times can sometimes be longer. Secondly the pipeline must be suitable for vacuum pressures.